15m² hardwall cleanroom for Dubai-based technology company
Connect 2 Cleanrooms was appointed to create a cleanroom solution to assist XPANCEO in developing smart contact lenses that displays images directly onto the eye.
The 5m x 3m hardwall cleanroom is the next step in allowing XPANCEO to further their research into technological advances and manufacturing processes.
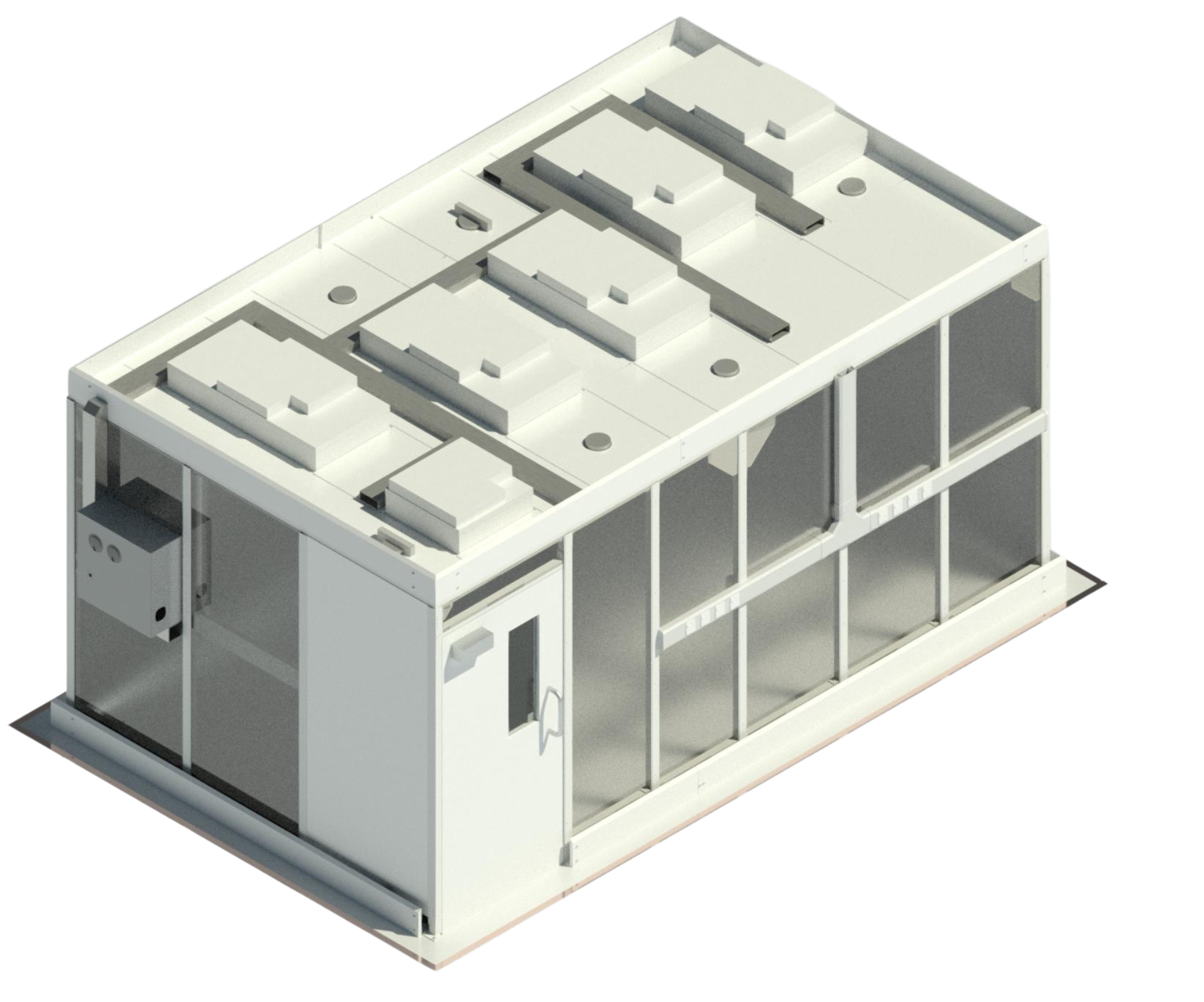
Key features of the cleanroom
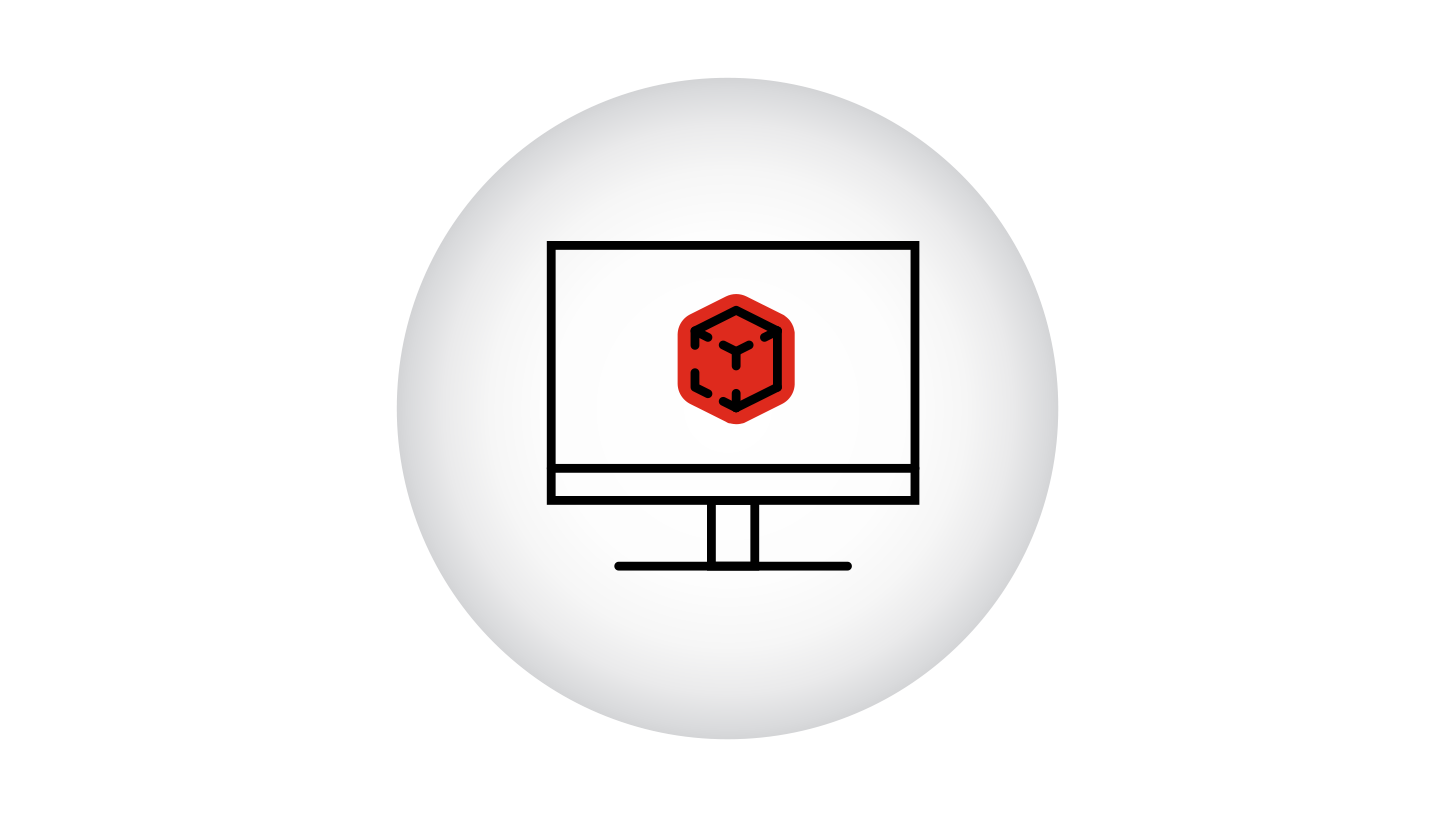
15m² hardwall cleanroom
ISO classes 6 and 7
Cleanroom consumables
Cleanroom validation
The client
XPANCEO, based in Dubai, is developing a smart contact lens that displays images directly onto the eye. Their goal is to merge all existing devices into one interface, enabling users to enjoy the most common apps and software they use on screens in infinite XR (extended reality), as well as monitor their health and receive comprehensive practical recommendations.
Understandably, the final product will be very small, meaning that many components need to be developed at nano level. These technologies include:
- Optical lithography:
- Photoresist processing – spin-coating, baking, developing.
- Pattern writing using maskless photolithography.
- Physical vapor deposition of thin metal and dielectric films via magnetron sputtering and e-beam evaporation.
- Sensitive materials processing in a glovebox (e.g. organic LED prototyping).
The cleanroom
The client initially had a draft of the cleanroom layout that included proposed equipment locations and planned activities, and there was an ISO Class 6 classification determined for the main production area, based on the equipment specifications that are to be used within the environment.
The hardwall cleanroom measures 5m x 3m, including a change area, internal and external plug sockets fitted, UV window protection to protect processes from UV light as well as yellow UV filters fitted to the lights inside.
The main area achieves ISO Class 6 and the change area ISO Class 7. The implementation has allowed XPANCEO to deepen their research on several components, including technology for IOP (intraocular pressure) sensing and eye tracking, as well as 2D electronics to power the smart contact lens.
Minimising the construction impact on the host building and facilities was a top priority to XPANCEO, and so as always, the Connect 2 Cleanrooms installation team took this into account from day one of construction working with the XPANCEO team, causing as little disruption as possible.
Once complete, the cleanroom was then validated by our team at rest, including tests such as particle counts, air volume tests and air change rate tests.
Cleanroom consumables
The client had a need for a range of equipment and materials and so the Cleanroomshop team advised on the most appropriate items to use within the environment. These included coveralls, hoods, shoe covers, masks, stationery and monitoring instruments such as particle counters and anemometers.
XPANCEO testimonial
We chose to work with Connect 2 Cleanrooms based on their extensive cleanroom construction experience, particularly on a global scale. The team assisted us with our initial draft of the cleanroom layout, ensuring the correct compliance was met throughout each area. The finished cleanroom in fact has a better class by air particulate on the level of ISO Class 5, which gives a good potential for higher quality processes and equipment upgrades we may work on in the future. We thank the Connect 2 Cleanrooms team for their support and professionalism throughout the project, and we look forward to working together into the future.