Monobloc Cleanrooms: Achieving Optimal Particulate Control and Contamination Prevention
Cleanrooms play a crucial role in industries where strict control of particulate contamination and cross-contamination risks is essential. Among the various cleanroom construction options available, monobloc cleanrooms stand out for their ability to provide superior particulate control and meet the rigorous standards of ISO 14644-1 and Good Manufacturing Practice (GMP).
The term “monobloc cleanrooms” specifically emphasises the concept of a unified or integrated structure, often referring to cleanrooms constructed with panels that have a seamless, flush, or semi-flush finish.
In this blog post, we will explore the advantages of monobloc cleanroom systems, focusing on their flush finish, minimal ledges, panel fabric considerations, and envelope integrity.
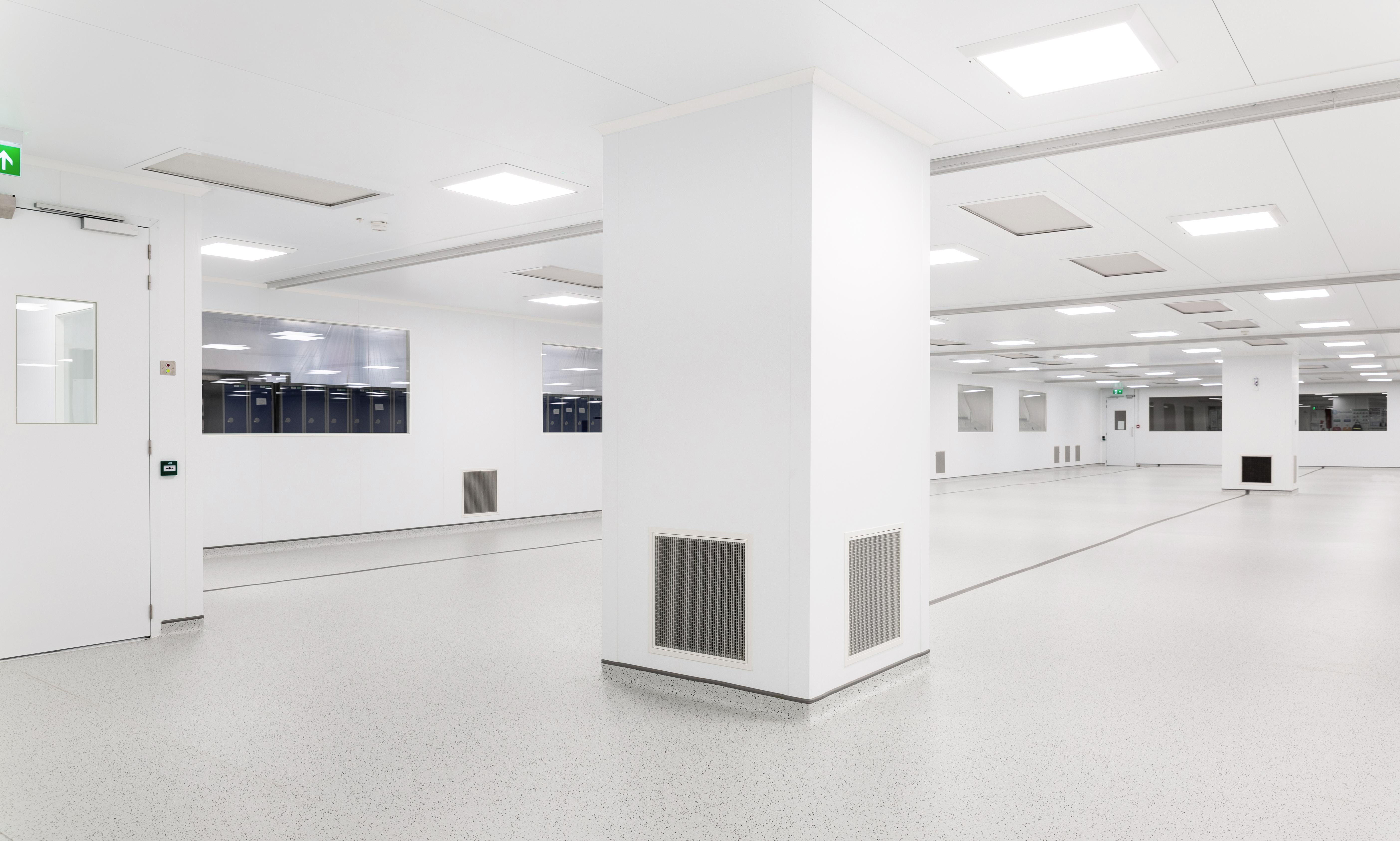
Flush cleanroom systems for enhanced particulate control
A significant advantage of monobloc cleanroom systems is their flush finish, eliminating trapping points and minimising the risk of particulate contamination. Flush cleanrooms ensure smooth surfaces without protrusions or recesses that could collect and harbour particles, making them ideal for industries such as pharmaceutical production, where stringent cleanliness standards are paramount. Monobloc cleanrooms offer the option to incorporate flush vision panels and doors, further enhancing the control of particulate contamination. GMP cleanroom construction principles emphasise the importance of minimising projecting ledges, as they can become potential sources of particulate contamination and hinder cleaning processes.
Semi-flush and full-flush finishes
Semi-flush and full-flush cleanroom finishes are both designed to help control contamination, but they have some key differences. The UltraTech Versatile semi-flush systems have a smooth finish with slight recesses around elements like wall panels and windows, which still makes cleaning easy and reduces particle build-up. A key benefit of using a semi-flush cleanroom over a fully flush system is cost-efficiency. Semi-flush designs still offer great contamination control and are easier to clean than standard finishes, but they are generally more affordable to install. They provide a high-quality, professional finish without the added complexity and expense of achieving a fully seamless surface, making them ideal for cleanrooms that don’t require the highest level of particulate control.
The UltraTech Precision full-flush systems go a step further by making all surfaces sit completely level in a seamless integration, with no visible gaps or edges. This creates a finish that’s easier to clean and is better at stopping particle buildup. Both options adhere to GMP guidelines, with semi-flush systems suitable for GMP grades C and D, and full-flush systems suitable for GMP grade B, as this offers a higher level of hygiene and is ideal for critical environments, such as pharmaceutical production.
Panel fabric considerations
When choosing the fabric for the cleanroom panel finish, there are several factors to consider. Cleaning regimes, robustness, and surface resistivity are among the key considerations. Different industries, such as battery, semiconductor, and microelectronics, have specific requirements for surface resistivity. Monobloc cleanroom systems offer flexibility in panel fabric choices, allowing for customisation based on the industry’s unique needs while ensuring durability and compatibility with stringent cleaning protocols.
Positive pressure control
Positive pressure is a fundamental principle in cleanroom design. By using specialised air handling systems and advanced HVAC technologies, monobloc cleanrooms can maintain a higher pressure inside the cleanroom compared to surrounding areas. This pressure differential acts as a barrier, preventing the ingress of particles and contaminants that may be present in adjacent spaces. The controlled positive pressure ensures that the cleanroom environment remains clean and free from external contamination sources.
Air recirculation and air return panels
Air recirculation is an essential aspect of cleanroom operation, contributing to the efficiency of air filtration and maintaining a clean and controlled environment. Monobloc cleanrooms incorporate air return panels strategically placed within the cleanroom facility to facilitate the recirculation of filtered air. The filtered air is drawn through these panels and recirculated back into the cleanroom environment, ensuring a continuous supply of clean and filtered air throughout the space to meet the particle count limits according to ISO 14644-1 and EU GMP guidelines.
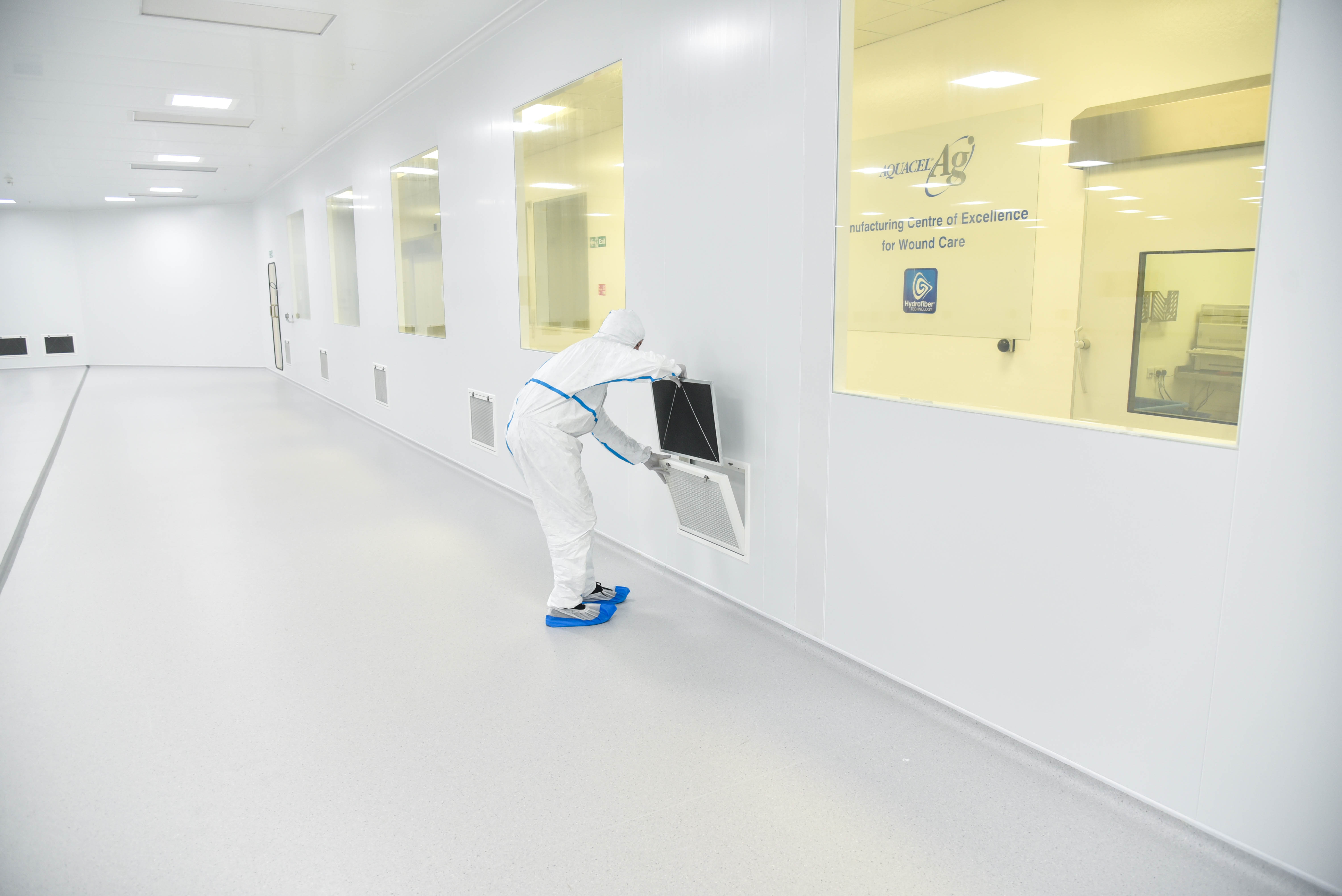
Envelope integrity and moisture protection
The building envelope plays a critical role in maintaining a controlled cleanroom environment. A fully sealed monobloc cleanroom panel system with airlocks and well-sealed doors provides superior envelope integrity. This level of protection insulates the cleanroom and safeguards it from moisture ingress. Moisture control is particularly crucial in industries where excess humidity can adversely affect product quality or compromise the integrity of sensitive equipment.
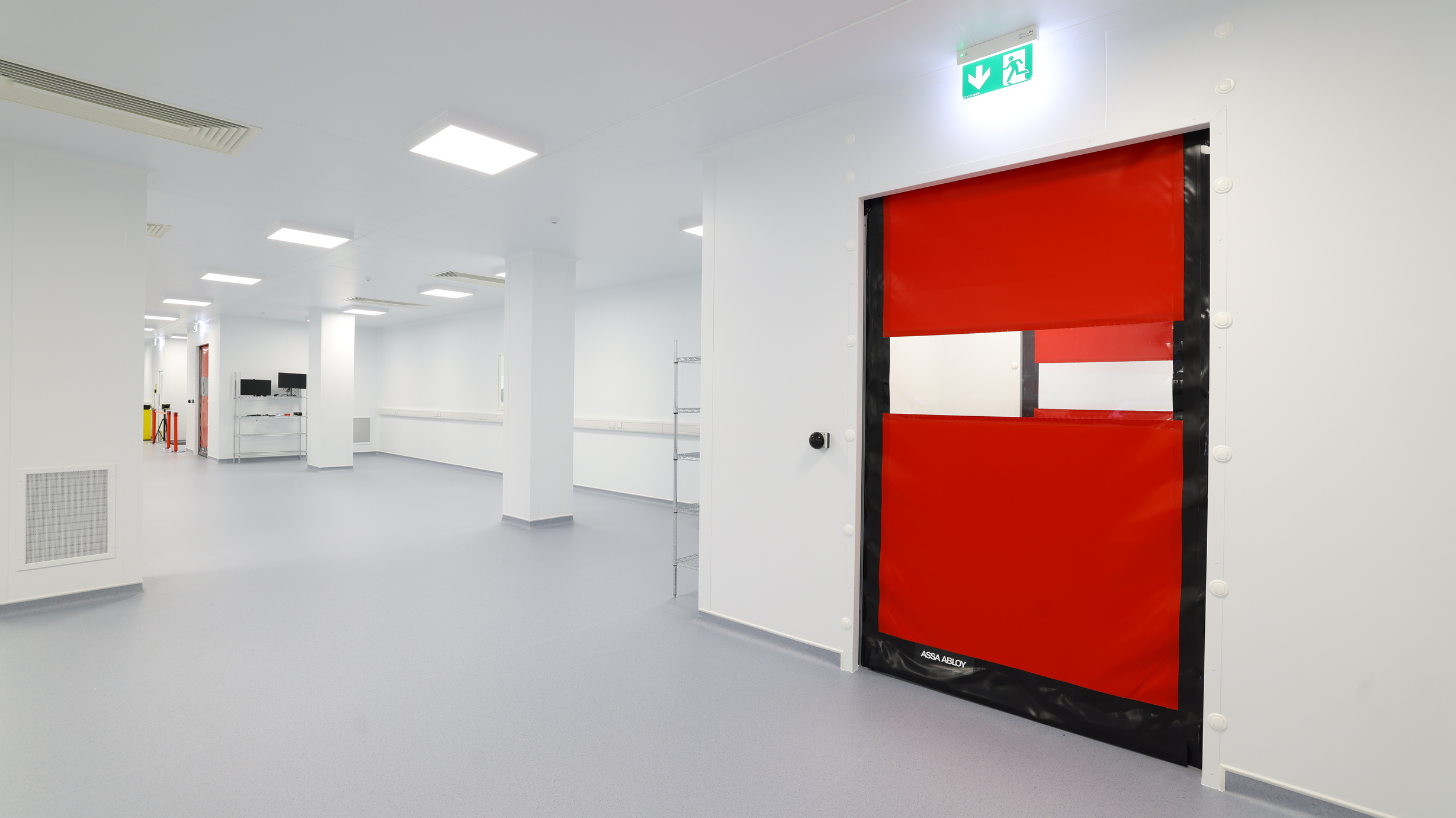
Monobloc cleanroom systems offer numerous advantages in achieving optimal particulate control and minimising contamination risks. These cleanrooms ensure superior control over particulate contamination with their flush finish, minimal ledges, and incorporation of flush vision panels and doors. Moreover, the choice of panel fabric and a fully sealed envelope further enhances the cleanroom’s robustness and protection against moisture ingress. By adopting monobloc cleanroom construction principles, pharmaceutical production, battery manufacturing, and microelectronics can maintain stringent cleanliness standards and ensure the highest product quality.
Related case studies
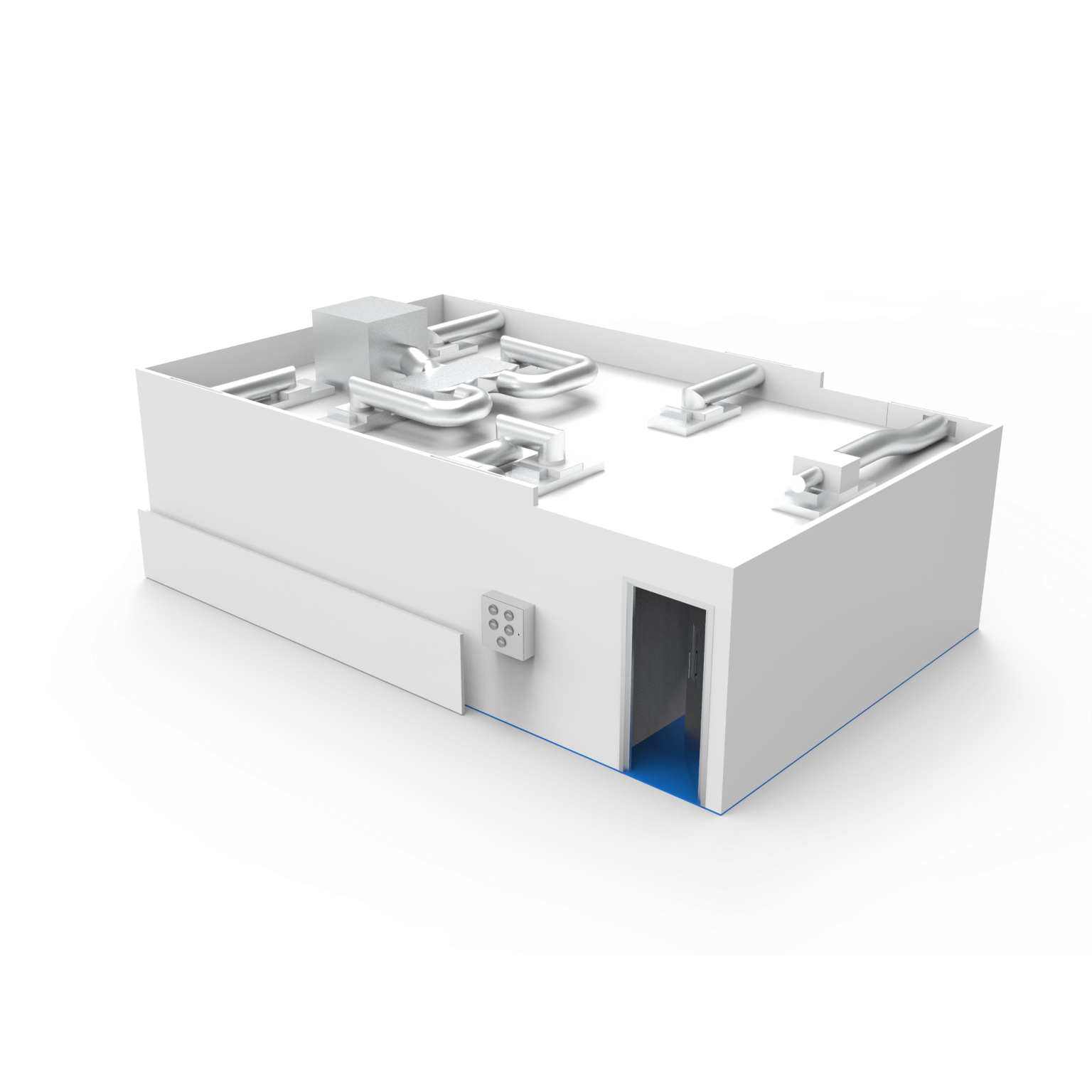
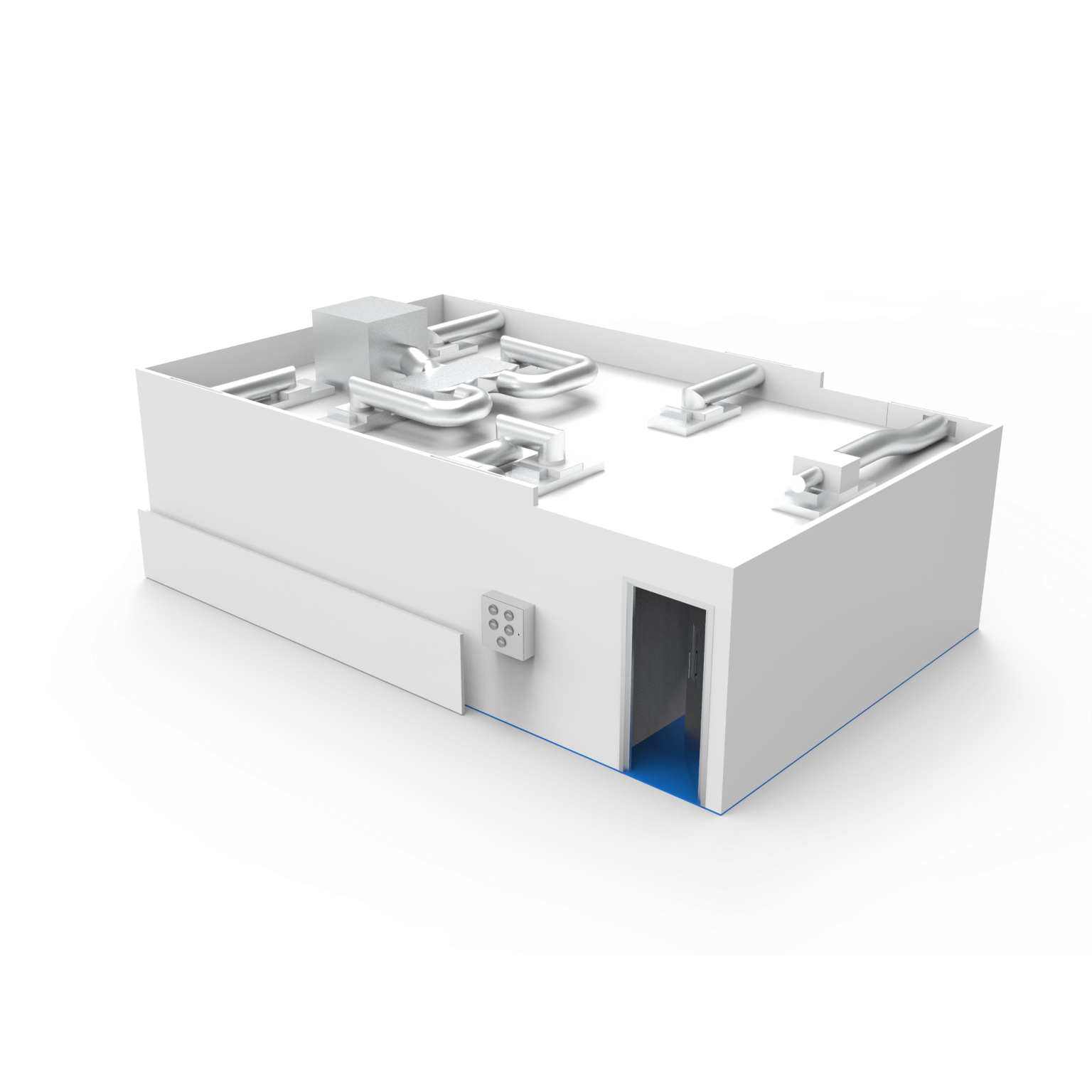
Start a project with us
Our design and build specialists have experience working with customers in all kinds of industries on a global scale, achieving great results time and time again. We’d love to work with you as well!