Softwall cleanrooms: Flexible controlled environments
Cleanrooms have become indispensable in industries that demand control over environmental conditions, to maintain high cleanliness levels.
While hardwall cleanrooms provide robust structures, softwall cleanrooms remain ever-popular due to their versatility and cost-effectiveness.
In this blog, we’ll look at what softwall cleanrooms are, the benefits of using them and their ideal applications.
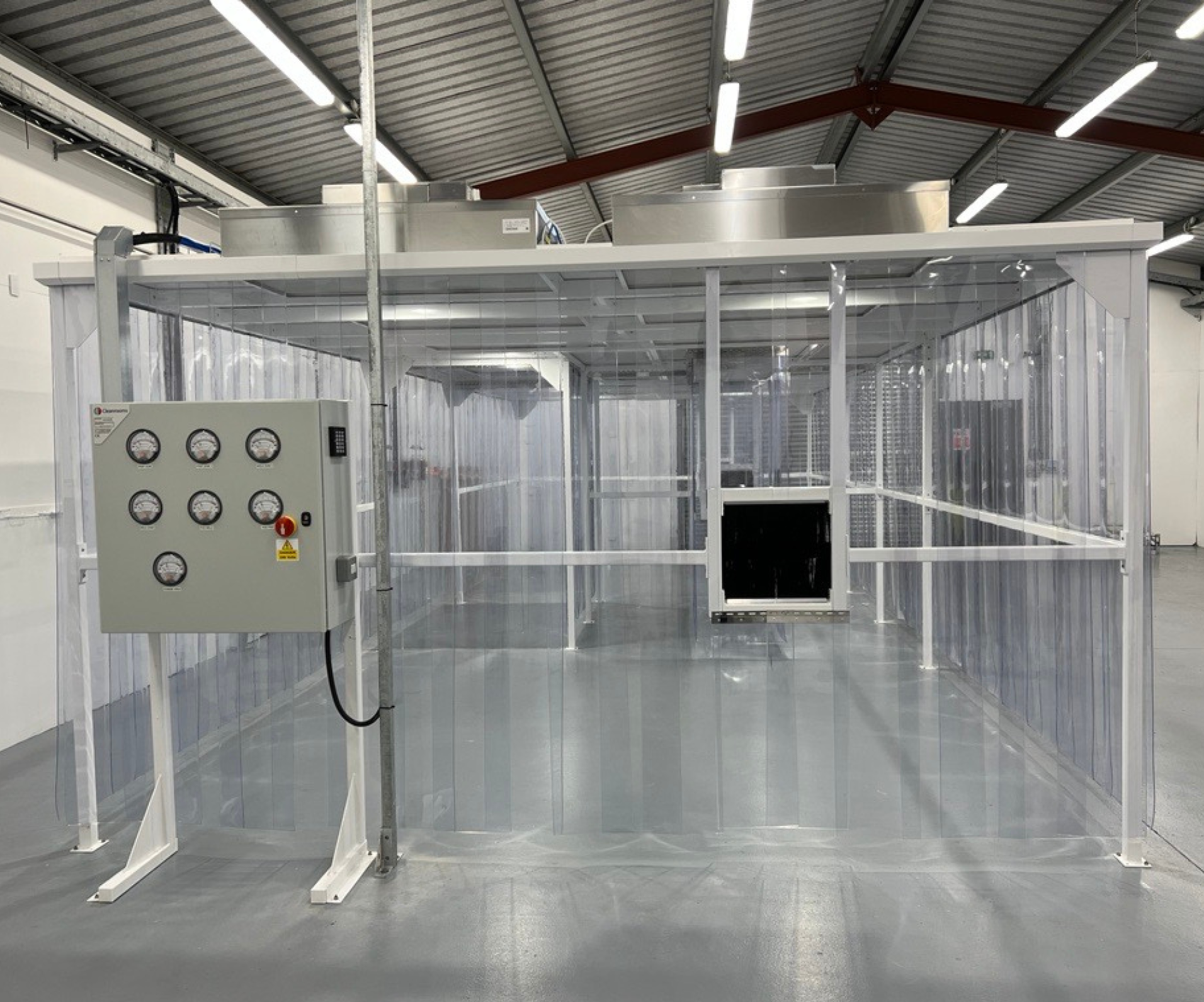
What are softwall cleanrooms?
Softwall cleanrooms are controlled environments that utilise flexible curtain strips, made from non-shedding materials, such as vinyl or PVC, to create a barrier against contaminants. These curtains or panels are typically suspended from a sturdy frame, allowing for quick and easy modification of the cleanroom layout.
Softwall cleanrooms are designed to maintain specific levels of air cleanliness, typically achieving an ISO class 7 or 8 environment, making them an ideal solution for manufacturing and industrial applications that need an element of environmental control. Due to their simple structure, they are one of the fastest cleanroom solutions to construct, making them an attractive option for anyone looking to modify their production environment in a tight timeframe.
Benefits of softwall cleanrooms
Cost-effective solution
Softwall cleanrooms offer significant cost advantages over their hardwall and monobloc counterparts. The flexible materials used in their construction are generally more affordable, resulting in lower initial setup costs. Additionally, softwall cleanrooms require a less complex infrastructure and are easier to install and modify, reducing ongoing maintenance expenses.
Versatility
Softwall cleanrooms excel in accommodating changing requirements and spatial constraints. The modular nature of softwall systems enables quick and hassle-free reconfiguration of the cleanroom layout to suit evolving needs. Whether you need to expand the cleanroom, create separate zones, or profile panels around additional equipment, softwall cleanrooms offer the flexibility to adapt easily.
Enhanced contamination control
Softwall cleanrooms employ state-of-the-art filtration systems to ensure optimal air cleanliness. HEPA or ULPA filters effectively capture and remove particles and micro-organisms from the air, minimising the risk of contamination. The soft, non-shedding curtains or panels further reduce particle generation, making them suitable for industries with stringent cleanliness requirements.
Energy-efficiency
Softwall cleanrooms are designed to be energy-efficient. The flexibility of the soft partitions allows for precise control of the cleanroom’s size, reducing the volume of air that needs to be conditioned. This results in lower energy consumption, cost savings and environmental benefits.
Softwall cleanroom applications
- Medical plastics: Softwall cleanrooms are widely used in medical plastic production, where maintaining strict cleanliness and particulate control is crucial. They provide an ideal environment for housing injection moulding machines and can be mounted on castors to give access to tool changes.
- Precision engineering: Fabrication, manufacturing, and production processes often require cleanrooms with adaptable layouts. Softwall cleanrooms enable any space to be upgraded into a clean environment, ensuring optimal environmental conditions for successful outcomes.
- Electronics: The electronics industry demands cleanrooms to produce sensitive electronic components. Softwall cleanrooms offer protection against particles and static discharge, making them suitable for applications such as PCB assembly, microelectronics, and semiconductor manufacturing.
- Medical devices: Softwall cleanrooms are used to manufacture medical devices to prevent contamination and ensure the safety and efficacy of the products. They provide controlled environments for assembly, packaging, and sterilization activities.
Case studies
Find out more about some of our softwall cleanroom projects:
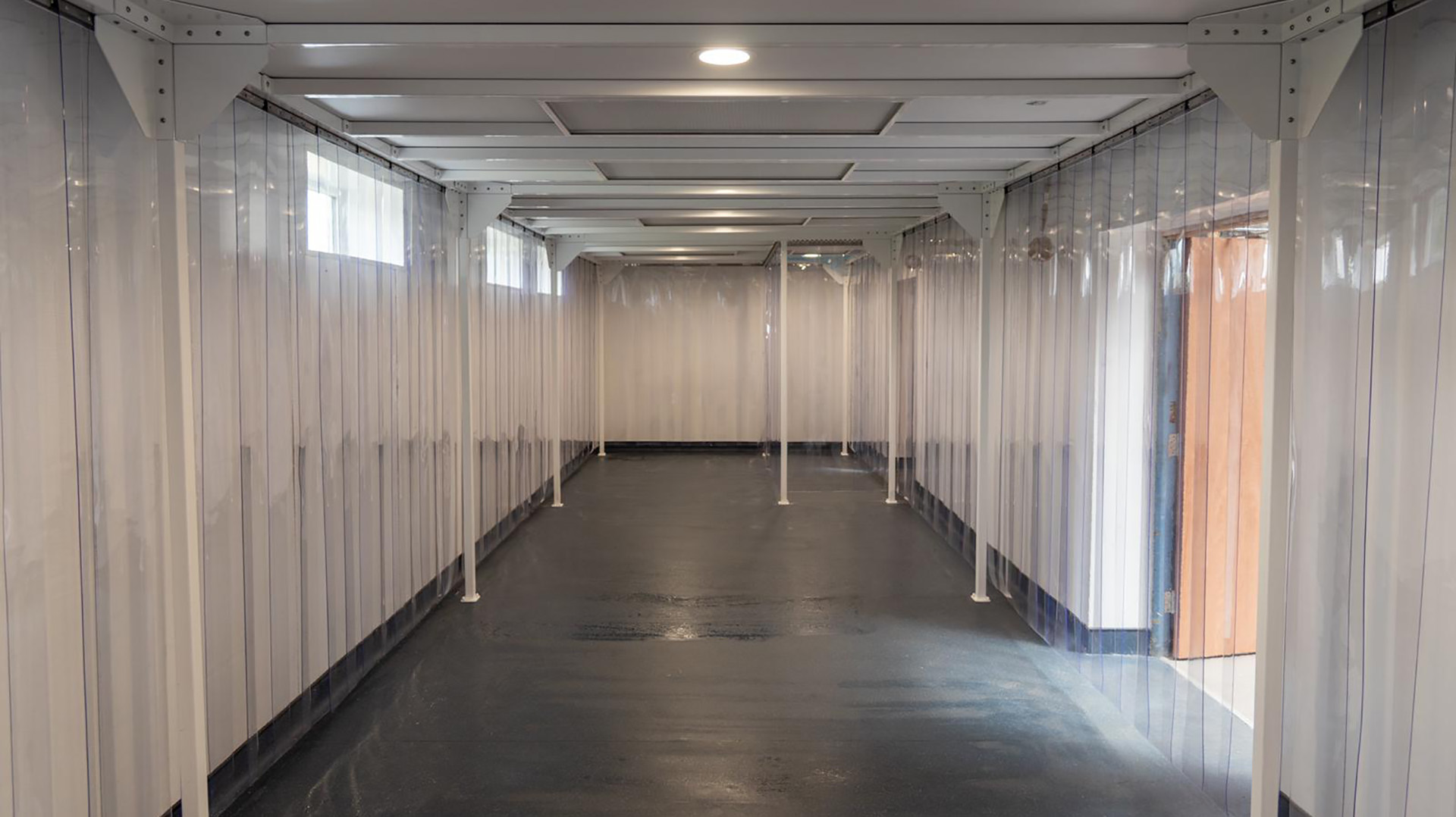
ISO Class 7 softwall cleanroom for AGMA
Connect 2 Cleanrooms delivered a softwall cleanroom for the manufacture of sterile wet wipes and dry wipes, for global pharmaceutical markets.
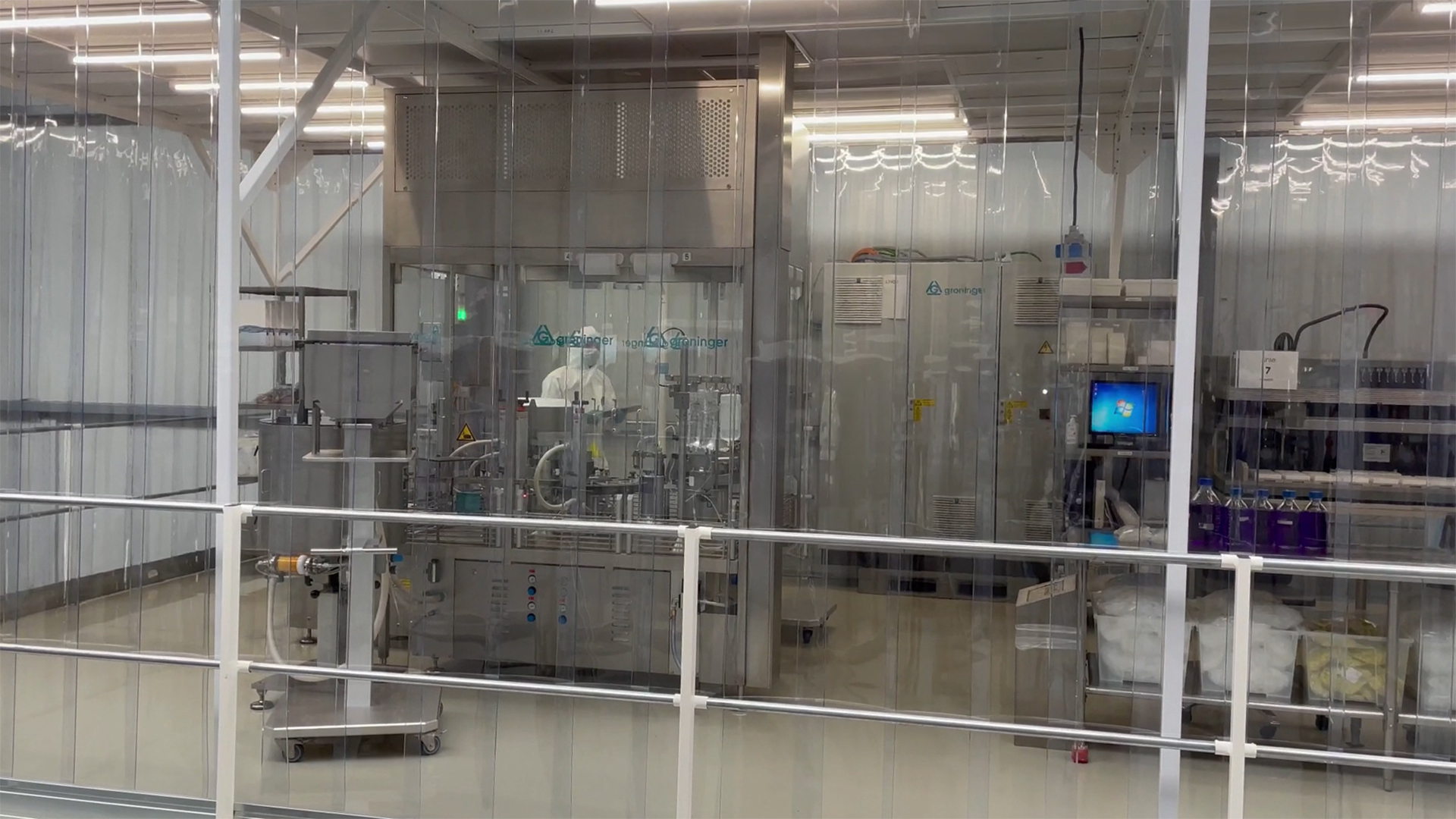
Softwall cleanroom for PCR test filling line
Connect 2 Cleanrooms was appointed to design and build an ISO 6 softwall cleanroom for contract filling specialists, Erkol Fill
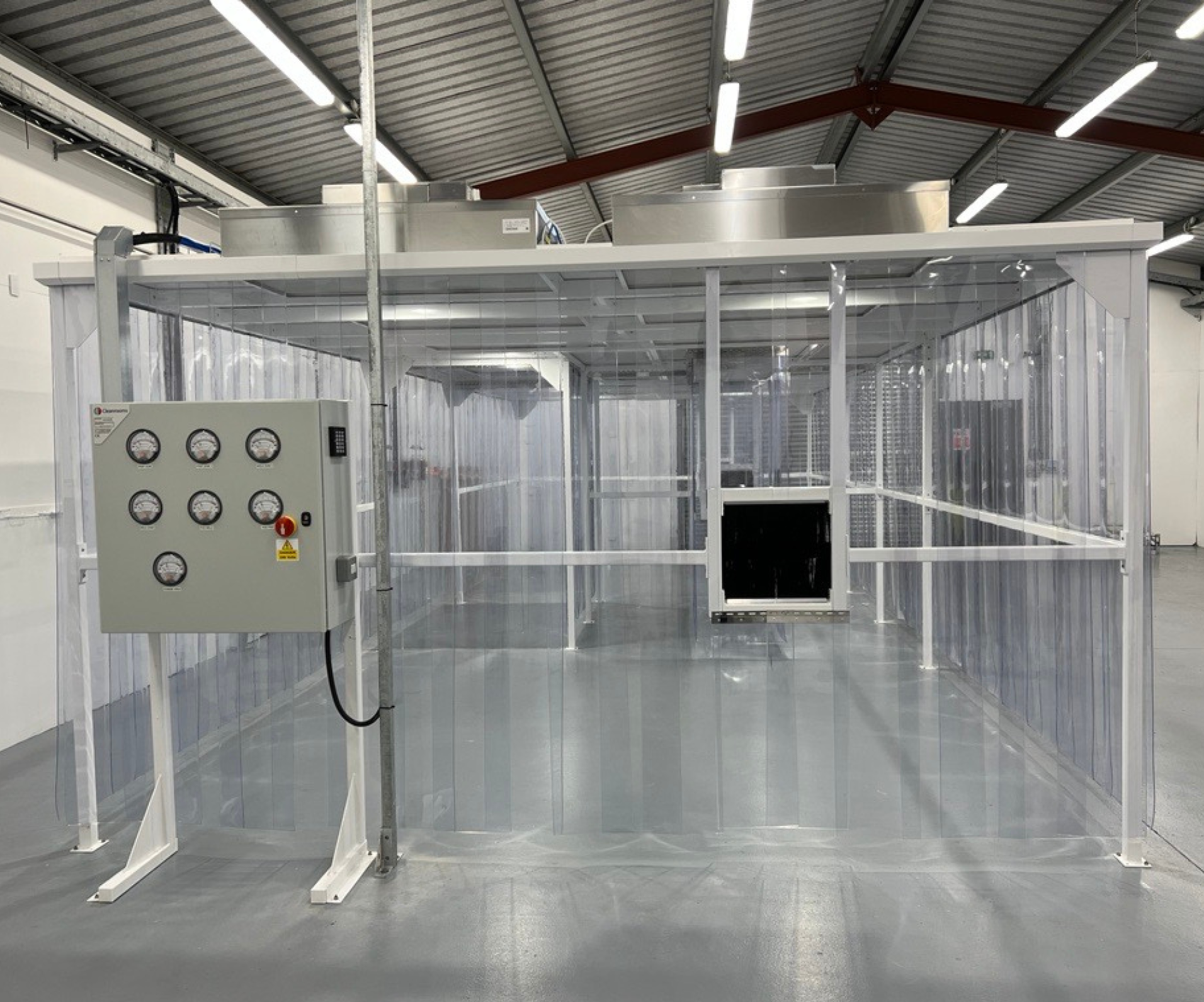
High-purity pipe fabrication cleanroom with ISO 4 pods
A custom-built ISO cleanroom from Connect 2 Cleanrooms was recommended to AE Global by another company in the industry.
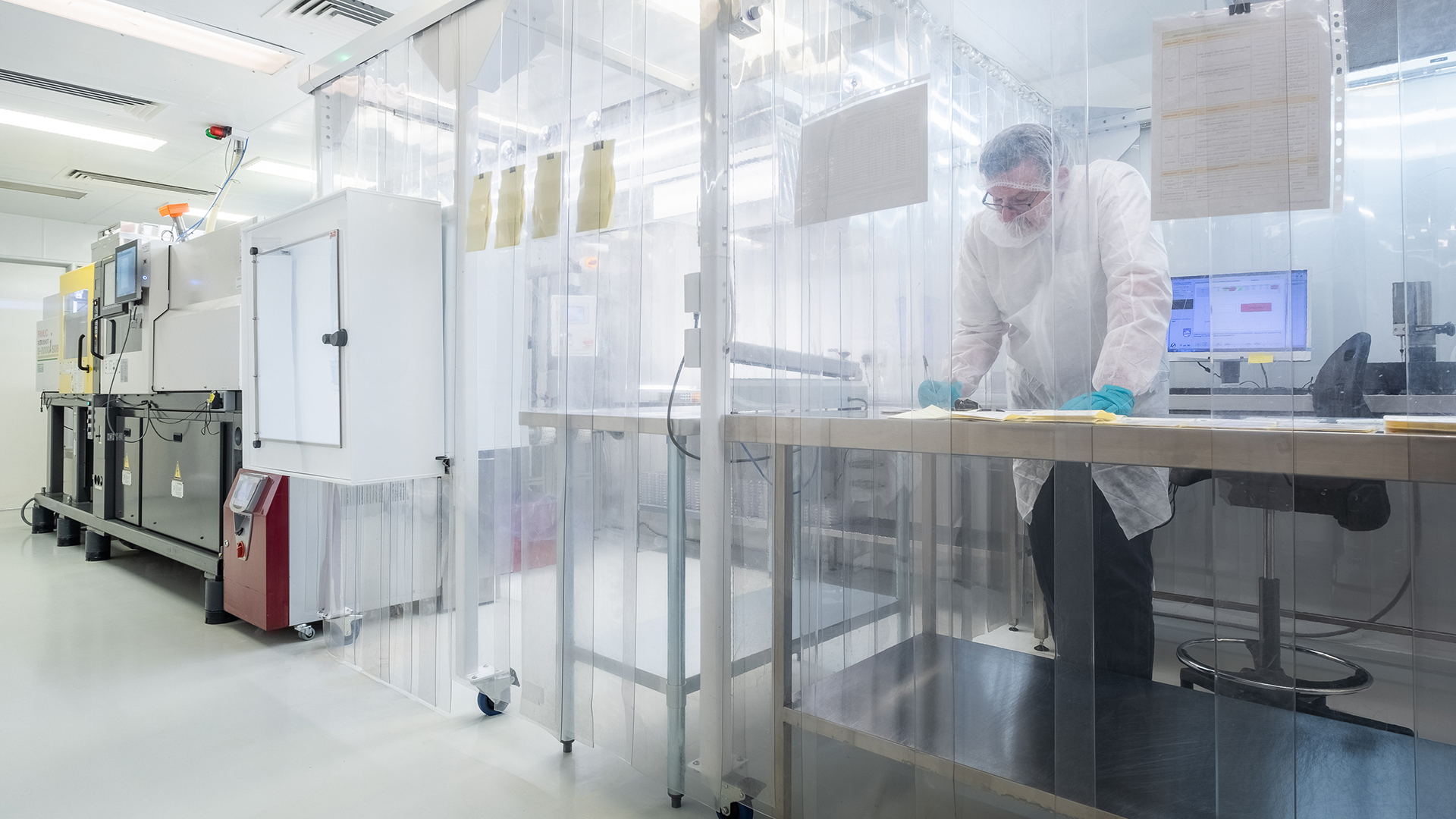
Modular cleanrooms to facilitate growth in the medical device market
Optimold Limited is a contract manufacturer producing injection moulded components for medical devices, such as auto-injectors, asthma inhalers, drug delivery and blood diagnostics for both hospital and laboratory use.
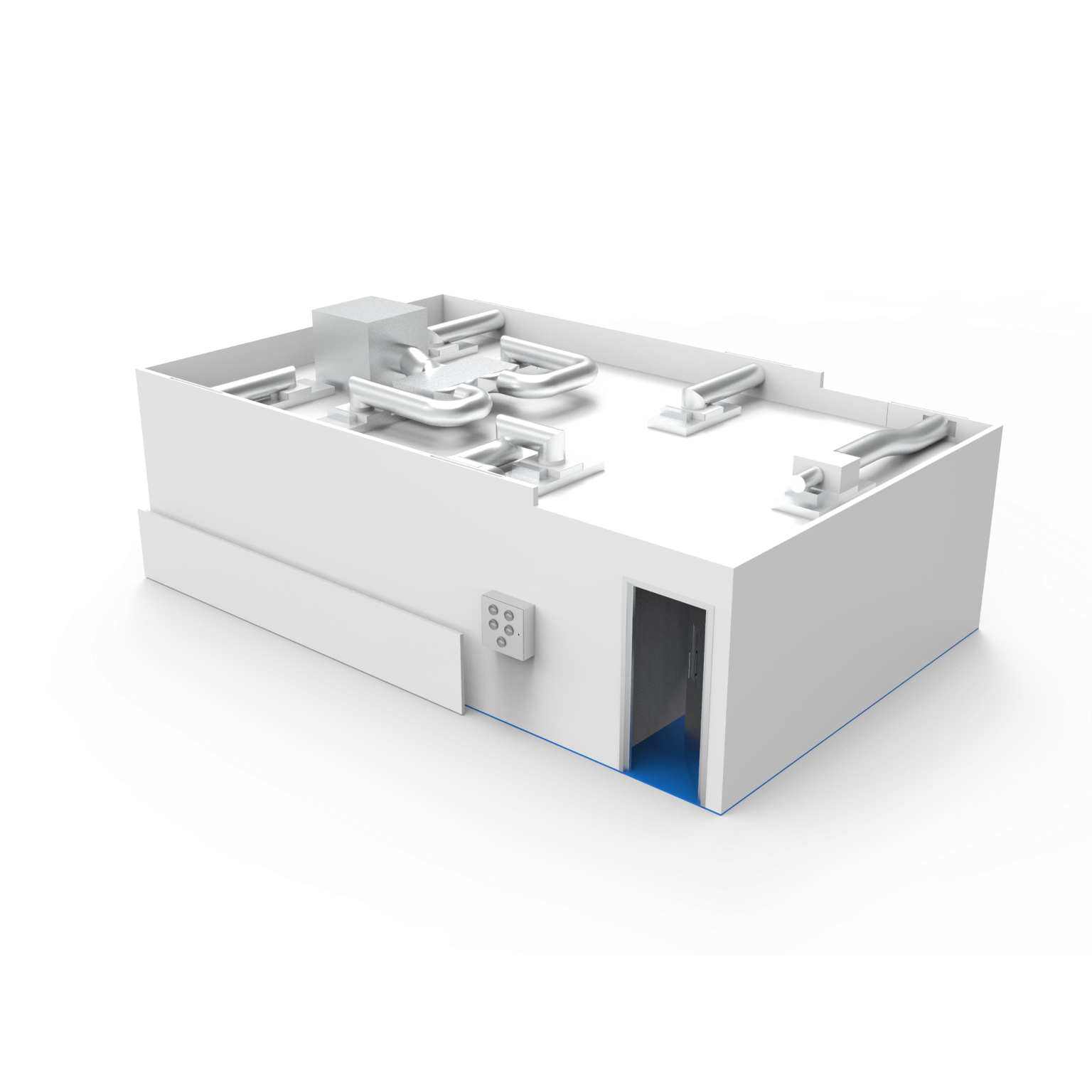
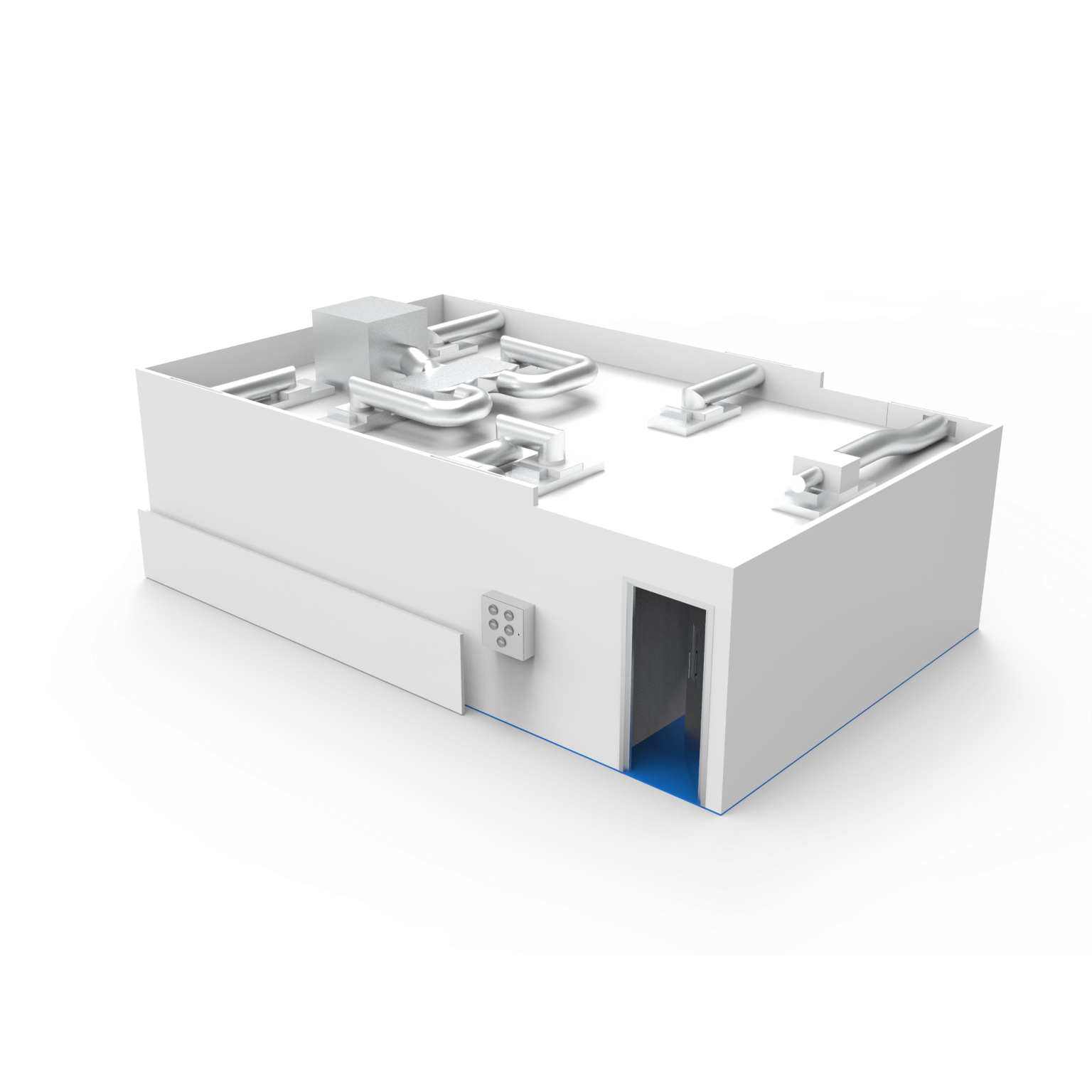
Ready to start a new project?
We are a modular cleanroom manufacturer. Our cleanroom design and build specialists have experience working with customers in all kinds of industries, achieving great results time and time again. We’d love to hear about your next project!