The Difference Between Cleanroom Qualification and Validation
Maintaining a contamination-free environment is a top priority for cleanroom users. Equipment, design, processes, and procedures all play a critical role in upholding the cleanliness and integrity of a controlled space – but how do you know these are performing as they should be? And if a contamination incident occurs, how do you identify the root cause? This is where cleanroom qualification and validation come in.
In this blog, we’ll break down the key differences between cleanroom qualification and validation, what they aim to achieve, and why they’re necessary to maintain the cleanliness and performance of a controlled environment.
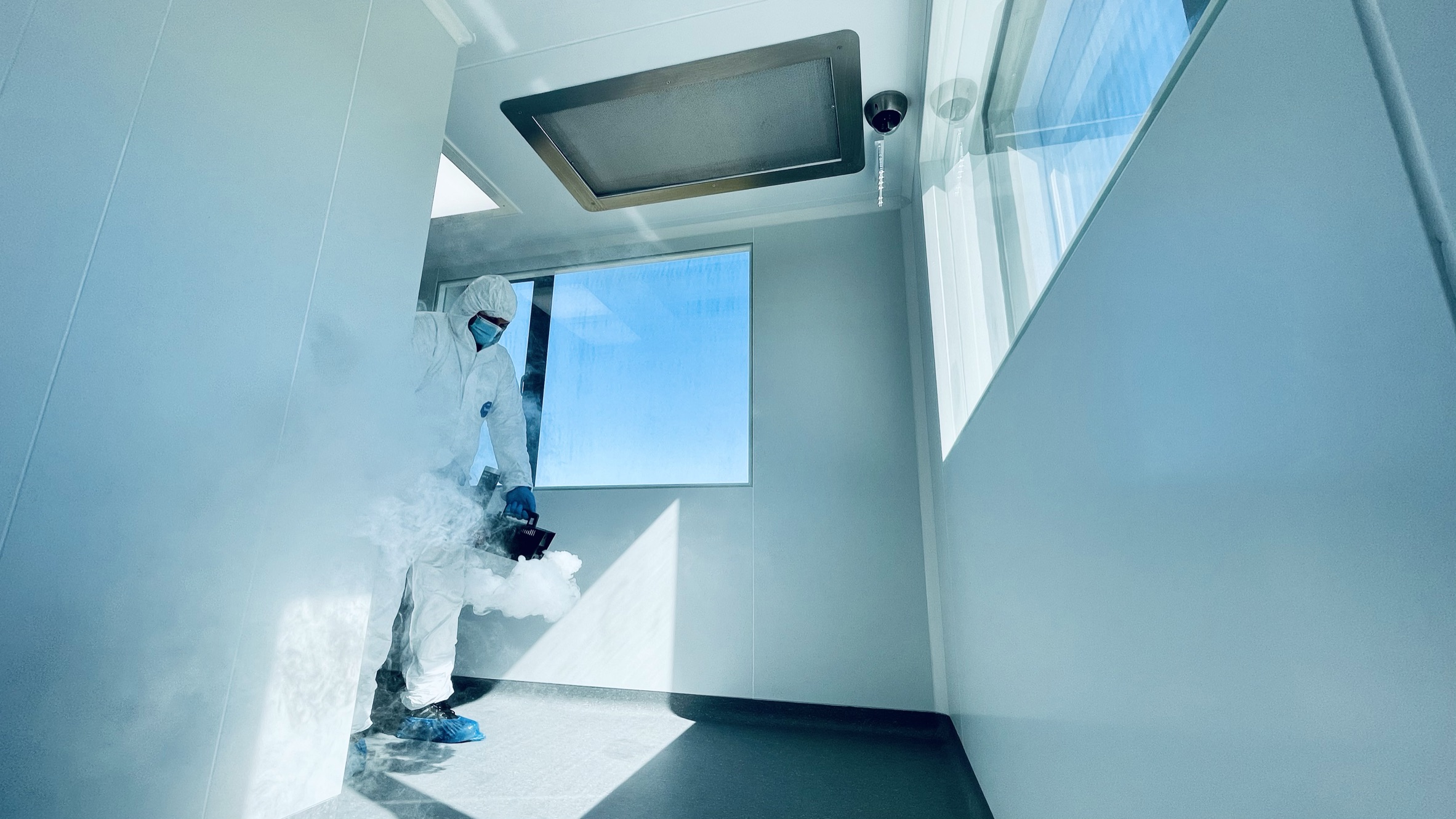
Cleanroom qualification vs validation
In the cleanroom industry, the terms qualification and validation are used to describe the testing and verification of a controlled environment’s performance. While the terms are often used interchangeably, in regulated industries including pharmaceuticals and biotech – particularly under GMP (Good Manufacturing Practice) – they have their own definitions and aims.
Qualification and validation are crucial processes in verifying a cleanroom meets its intended purposes and regulatory requirements. Qualification is the specific verification that any facilities, equipment, and utilities are performing as they should be and meet regulatory requirements. Whereas validation is the specific verification that any procedures, processes, and activities carried out in the cleanroom are consistent and correct.
What is qualification?
Cleanroom qualification specifically aims to ensure that a cleanroom is built and working correctly under both ‘at rest’ (with no personnel or equipment running) and ‘in operation’ (operating normally with personnel present and equipment running) conditions.
A cleanroom qualification verifies and documents that the entire controlled environment is performing as it should be without compromises to the design or equipment it holds.
Qualification is required during the build of the cleanroom, with periodic requalification a minimum of once per year following a risk-based approach to the intervals between each requalification. This ensures the cleanroom continues to meet the design and performance requirements. Qualification testing covers the following elements against the User Requirement Specification (URS):
- Design (DQ): Performed during the cleanroom’s design phase, evidencing that the design meets the URS and regulatory requirements.
- Installation (IQ): Performed following the build of the cleanroom, reviewing the architectural and functional components and gathering of commissioning reports to demonstrate the installation matches the URS and proposed design.
- Operation (OQ): Verifies the cleanroom operates as it should during the ‘at rest’ state, ensuring the system is operating as designed.
- Performance (PQ): Verifies the cleanroom operates as it should during the ‘in operation’ state, with all equipment running and personnel carrying out (or simulating) tasks.
Regulatory EU guidelines state that where possible, the below tests should be carried out as part of the cleanroom qualification process:
- Particle counts
- Filter integrity
- Airflow tests – velocity and volume
- Pressure differentials
- Airflow visualisation
- Microbial contamination
- Temperature and humidity
- Recovery testing
- Contamination testing
What is validation?
Validation specifically aims to ensure that the wider process (that can include a cleanroom) is performing correctly and consistently.
Validation is typically performed following the build and qualification of the cleanroom, with revalidation required in the event of any significant changes to the process, such as changes to the cleanroom or new equipment being installed. However, it’s best practice to revalidate your cleanroom environment every 12 months.
Validation tests can include the verification of:
- Gowning process of cleanroom users
- Particle monitoring
- Cleaning procedures
The key differences of cleanroom qualification and validation
Aspect | Qualification | Validation |
---|---|---|
Focus | Cleanroom design, installation, and functionality against the required specification | Overall performance of the cleanroom in use, as part of a wider process |
Questions it answers | Is the cleanroom built and working correctly? | Does the cleanroom perform consistently in practice to support the overall process being validated? |
Scope | Room structure, HVAC, filters, equipment, and utilities | Environmental control, procedures, personnel, behaviour |
Standards involved | EU GMP Annex 1 and 15, ISO 14644 (1 - 4) | EU GMP |
Performed | During cleanroom set up or modification | During new processes or major changes |
Types of testing | DQ, IQ, OQ, PQ, FAT and SAT, Requalification | Process validation, particle monitoring, cleaning validation, computer system validation |
Requalification or revalidation* | GMP grades A and B/ISO class 5 - 6: every 6 months | GMP grades C and D/ISO class 7 - 8: every 12 months | Following any significant changes or during risk-based time intervals - however, best practice every 12 months |
*Whilst there are requalification guidelines set out by GMP and ISO, these can also be triggered by implementing any cleanroom upgrades, changes to the cleanroom’s layout or equipment, process changes, or following any contamination incidents.
The benefits of requalification and revalidation
Cleanroom qualification and validation is vital for regulatory compliance and identifying potential issues within your controlled environment before a contamination incident occurs. Cleanroom qualification is mandatory for GMP cleanroom environments, specifically pharmaceutical facilities. However, it’s recommended that all businesses with cleanrooms should implement qualification and validation procedures.
Cleanroom requalification and revalidation can help you to:
- Detect and identify the source of harmful contaminations quickly and efficiently.
- Reduce operational downtime and maintenance costs.
- Remain compliant with regulatory requirements, industry standards, and guidelines including ISO and GMP.
- Support the quality, reliability, and consistency of a cleanroom, ensuring manufactured products are safe.
- Improves operational efficiency, performance, and workflows.
Overall, qualification and validation are terms often used interchangeably within the cleanroom industry, yet they’re two distinct testing protocols of cleanroom environments.
Qualification is verifying the cleanroom, with systems being suitable and functional for its intended use, covering aspects across design, installation, operation, and performance. Validation is ensuring that the entire cleanroom operations consistently meet standards during actual use.
Whilst qualification and validation have specific focuses and scopes, they ultimately aim to evidence the integrity of a controlled environment, reduce the risk of contamination, and ensure manufactured products are safe and up to standard.
Looking to qualify your cleanroom and validate your processes? Connect 2 Cleanroom’s in-house team of experienced technicians are CTCB-i certified to perform qualification and validation testing services on your controlled environment. For more information, speak to one of our experts below!